LAMINATED TUNNEL
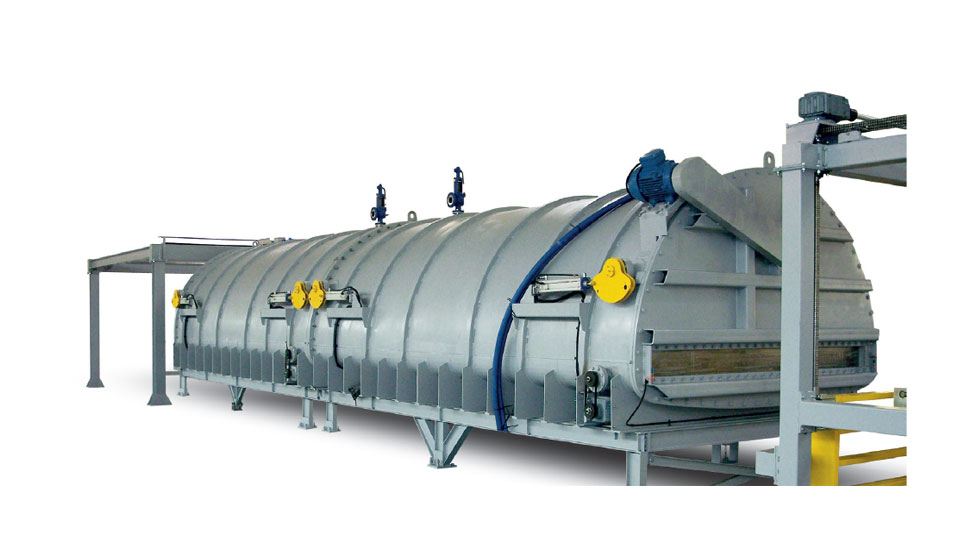
Laminating Tunnel
Revolutionary patented technology composed by n. 2 chambers: the first one for heating and the second one for cooling, both under pressure. One tray can be processed into the heating chamber and a further one into the cooling chamber simultaneously.
This two-chamber system ensures high energy saving and incredibly short cycle time, providing the best market ratio for output/production cost.
Highlights
Laminating Tunnel is arranged for standard PVB (interleaved or refrigerated), EVA and ionomer interlayers such as SentryGlas
.. It runs at 1 bar only above atmospheric pressure and guarantees the same quality results of finished product as those ones obtained by using a high pressure autoclave.
Heating system by means of electric resistances and through forced air recirculation system by special fan.
A second fan is placed on cooling chamber for cooling process, which is carried out through cooling battery and evaporating tower system.
Vacuum process with automatic connection and control system to laminate glass with flatness out of allowed tolerances.
Pressurizing and depressurizing system controlled by PLC according to the set recipe.
Horizontal glass processing for ensuring the best glass load optimization.
Multilevel buffer (up to eight positions) or crane system at tunnel entry and exit to load and unload all trays automatically.
Long-life silicone blankets ensure a cost effective solution comparing to traditional disposable bags normally used in vacuum process within high pressure autoclave.